Wiki¶
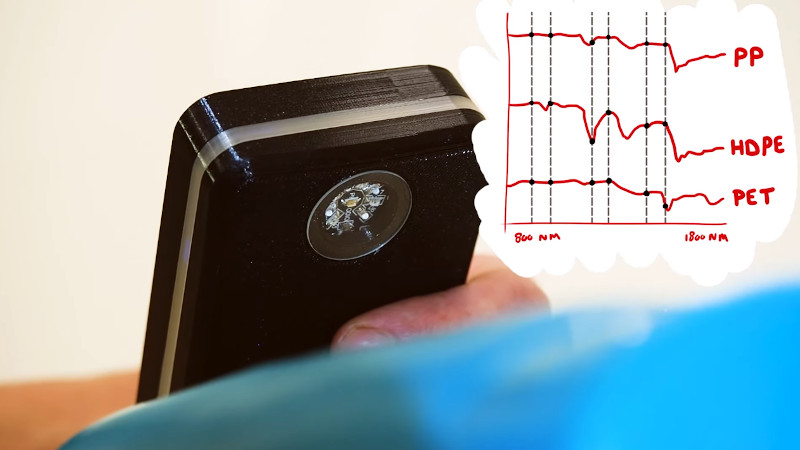
image: hackaday.com
Porteurs du projet:
- Aela Fortun (IUT mesure physique)
- Matthieu Pedros (IUT SGM)
- pgp (Fablab)
Renseignements: fablab@iut.u-bordeaux.fr
Synopsis¶
C'est un projet initialement lancé avec des étudiants de 2ème de BUT Mesures Physiques (2023/2024) puis repris en 3ème année par un autre groupe d'étudiants (2024/2025).Le but est de construire un scanner à plastique utilisant le NIR (Near Infra Red) comme celui ci:
- site officiel
- Présentation du projet sur hackaday
Le plastic scanner sera développé dans le but d'être exploiter dans le milieu professionnel par la suite, dans des centres de tri par exemple pour faciliter le recyclage final en identifiant la composition des déchets (2024/2025).
Conception¶
Cahier des charges
Bibliographie
Journal de bord
Test de la solution existante
Améliorations sur la branche cohabit
Améliorations du boîtier
Fabrication¶
Fabrication du boitierFabrication du boitier
Le boîtier est conçu pour abriter tous les composants essentiels de notre plastic scanner, notamment le circuit imprimé, l'écran OLED et la carte Arduino. Chacun de ces éléments est solidement fixé à l'intérieur du boîtier, assurant leur stabilité ainsi que leur protection contre les chocs et les éléments extérieurs. En plus de sa fonction protectrice, le boîtier joue un rôle crucial dans la manipulation de l'appareil. En regroupant tous les composants en une seule unité compacte et ergonomique, il permet une utilisation facile et pratique de l'appareil de mesure. Ce design intégré optimise non seulement la durabilité des composants, mais améliore également l'efficacité du plastic scanner. Le boîtier a été totalement refais par les 3èmes années pour améliorer l'ergonomie et réduire les entrées de lumière non souhaitées qui pourraient fausser et augmenter les incertitudes de mesure déjà importantes.
Techniques employées :¶
- Impression 3D
- Découpe laser
Logiciels utilisés :¶
- Solidworks
- FreeCAD
- eDrawings
Objectifs :¶
le boitier du scanner doit répondre à plusieurs contraintes :- Avoir suffisamment de place à l’intérieur pour le circuit-imprimé et la carte Arduino
- Avoir des trous pour laisser les LEDs, écran et boutons visibles
- Être facilement démontable
- Être pratique et facile à manipuler
Fichiers relatifs à la fabrication :¶
Part | Fichier | Observation | Image | _.Date |
---|---|---|---|---|
Freecad | 2024-06-11_plastic-Scanner.FCStd | fait | ![]() |
juin 2024 |
Plan de découpe | découpe sup inf.DXF | fait | |
|
Plan de découpe | plan_déoupé.svg | fait | |
Description et Fichiers relatifs à la fabrication du nouveau boîtier (2024/2025):¶
Le boîtier a été repensé pour n'être plus qu'en deux parties, entièrement faites à l'imprimante 3D. Des inserts en acier ont été ajouté de manière à pouvoir visser la carte aux deux parties du boîtier et pouvoir la dévisser quand on le souhaite. De plus, les dimensions ont été revues car précédemment aléatoires, le boîtier est plus robuste et rigide, l'écran à été intégré et les boutons ont été supprimés car il nécessaire que l'appareil soit branché à un ordinateur pour fonctionner, on le pilotera donc depuis celui-ci. Voici les fichiers des modèles des différentes pièces du boîtier, pour pouvoir le modifier ou l'imprimer directement (voir fichiers en bas de page).
Démarche et analyse du résultat :¶
Pour la conception du boîtier, nous avons utilisé le logiciel SolidWorks, qui nous a permis de modéliser précisément toutes les caractéristiques nécessaires pour intégrer les composants du plastic scanner. Afin de transférer les modèles créés dans SolidWorks à l'imprimante 3D, nous avons utilisé FreeCAD comme outil intermédiaire, facilitant la conversion des fichiers et leur préparation pour l'impression.
Pour la fabrication du boîtier, nous avons employé une imprimante 3D capable d'imprimer en PET recyclable, un matériau choisi pour ses propriétés écologiques et sa durabilité. Cette technologie d'impression nous a permis de créer un boîtier robuste et sur mesure, parfaitement adapté à nos besoins.
En parallèle, pour la découpe des parties supérieures et inférieures du boîtier, nous avons utilisé le logiciel eDrawings. Cette étape de découpe laser était essentielle pour créer des ouvertures précises, permettant l'accès aux deux boutons du circuit imprimé, à l'écran OLED, et pour garantir que les LED puissent fonctionner correctement sans obstruction. Grâce à cette approche détaillée et méthodique, nous avons réussi à produire un boîtier à la fois fonctionnel, esthétique et pratique pour notre appareil de mesure. (voir 2024-06-11_plastic-Scanner.FCStd)
Au niveau du plan de découpe, il était crucial de concevoir une partie du boîtier avec des ouvertures permettant d'accéder aux boutons utilisés pour lancer l'acquisition du scanner. Nous devions nous assurer que ces ouvertures soient suffisamment grandes pour permettre à l'utilisateur de passer ses doigts et d'appuyer facilement sur les boutons.
Cependant, nous avons rencontré un problème lors de l'assemblage. Par inadvertance, nous avons inversé les deux parties du boîtier, ce qui a conduit à une erreur dans le positionnement des ouvertures. Concrètement, les trous permettant d'accéder aux boutons ont été découpés sur la partie inférieure du boîtier au lieu de la partie supérieure.
Pour remédier à cette situation, nous avons pris la décision de conserver la partie inférieure du boîtier, qui inclut déjà les ouvertures permettant l'accès aux boutons. Ensuite, nous avons simplement refait le plan de découpe pour la partie supérieure, en veillant cette fois à bien positionner les ouvertures nécessaires pour permettre l'accès aux boutons.
Fabrication du PCBFabrication du PCB
Le circuit imprimé est le centre névralgique du plastic scanner. Il est conçu pour accueillir et exécuter le programme informatique qui contrôle toutes les opérations de l’appareil de mesure. En tant que véritable cœur électronique de notre système, le circuit imprimé assure la gestion précise des signaux électriques. Ces derniers sont cruciaux pour réaliser avec exactitude l'acquisition des mesures, le traitement des informations obtenues, ainsi que l'interprétation des valeurs d'absorbance spécifiques à chaque échantillon de plastique analysé.
Techniques employées :¶
- Gravure
- Perçage
- Plaquage
- Soudure
Logiciels utilisés :¶
- KiCAD Shematic Editor
- KiCAD PCB Editor
Objectifs :¶
Le circuit-imprimé permet :- La connexion et mise en fonctionnement de l’ensemble des composant (Arduino UNO, écran OLED…)
- L’alimentation de l’appareil de mesure
- L’acquisition des mesures d’absorbance (photo-diode)
Fichiers relatifs à la fabrication :¶
Part | Fichier | Observation | Image | _.Date |
---|---|---|---|---|
Kicad | PCB v2.kicad_pro | à tester | ![]() ![]() |
juin 2024 |
Démarche et analyse du résultat :¶
Premièrement, nous avons dressé la liste de tous les composants nécessaires à la création de l’appareil de mesure. Ensuite, à l’aide du logiciel KiCAD Schematic Editor, nous avons élaboré le schéma électronique du circuit imprimé, définissant l'ensemble des signaux électroniques inter-composants (terre, VCC, SDA, SCL, etc.). Deuxièmement, nous avons créé la représentation numérique du circuit imprimé (PCB), positionnant chaque composant à son emplacement final, avec les dimensions appropriées, et les reliant par des pistes de cuivre. Grâce aux équipements du département GEII, le motif du circuit a pu être ensuite imprimé sur un film photosensible appliqué sur une plaque de matériau isolant recouverte de cuivre. Après exposition à la lumière UV, les zones non protégées sont révélées et une solution de gravure élimine le cuivre exposé, laissant intactes les pistes de cuivre protégées. Les trous pour les composants sont ensuite percés, les vias sont métallisées afin de relier les deux couches du circuit imprimé. Une couche de protection, en étain, est appliquée pour protéger les pistes de cuivre de la possible oxydation. Enfin, le circuit imprimé subit des tests électriques pour vérifier la continuité et l'absence de courts-circuits.
Pour rendre notre appareil de mesure entièrement portable, nous avions initialement prévu d'intégrer une batterie. Cependant, lors de la réalisation du circuit, nous avons constaté que l'ajout de cette batterie nécessiterait beaucoup d'espace et un temps considérable pour connecter correctement tous les composants. En raison de ces contraintes et du temps limité dont nous disposions, nous avons décidé de ne pas inclure le système de batterie portable. À la place, nous avons opté pour une solution plus simple en alimentant l'ensemble des composants directement via la carte Arduino, ce qui nous a permis de simplifier le design et de respecter l’échéance.
Pour l'avenir du projet, il serait avantageux d'explorer des options pour réintroduire un système de batterie portable. Cela améliorerait considérablement la portabilité et l'autonomie de l'appareil, le rendant plus pratique et adaptable à diverses situations d'utilisation. L'intégration d'une batterie portable bien conçue permettrait non seulement de répondre aux besoins de mobilité des utilisateurs, mais également de rendre l'appareil plus flexible et autonome, sans dépendre d'une source d'alimentation externe.
Propriétés spectroscopiques des plastiquesPropriétés spectroscopiques des plastiques
Grâce à l'analyse spectroscopique approfondie de nos cinq échantillons de plastiques (PVC, PS, PP, PET et PEHD), nous avons pu identifier et comprendre les propriétés uniques de chaque matériau. Chaque type de plastique présente des propriétés spectroscopiques distinctes, absorbant à des longueurs d'onde spécifiques. Cette capacité nous permet d'utiliser notre plastic scanner pour différencier précisément un type de plastique d'un autre, facilitant ainsi le tri et le recyclage efficace des matériaux.
Démarche utilisée (2024/2025) :
Analyse spectroscopique de 7 plastiques différents de manière à couvrir un maximum de plastiques communs présents dans le commerce. Nous observons les pics d'absorption pour des échantillons purs que nous comparons avec des échantillons ayant subits un vieillissement accéléré pour identifier la présence du plastique en question dans le solvant dans lequel il reposait ( javel, acide, eau salée). Cela permet de simuler la réalité de la dégradation des déchets plastiques dans la nature, montrant l'importance du tri et du recyclage de ceux-ci pour éviter leurs présences dans l'environnement. Les déchets plastiques se dégradent en microparticules, des microplastiques qui nuisent fortement aux écosystèmes dans lesquels ils se retrouvent.
Aussi, chaque LED du Plastic Scanner a été analysée au spectromètre (allant jusqu'à 1100nm) pour identifier leur plage d'émission. La LED 7 émet un rayon vert aux alentours de 580 nm alors qu'elle émet théoriquement à 1650nm et ne devrait donc pas être visible. Un fichier détaillant ces analyses est disponible dans la documentation.
Techniques employées :¶
- Spectroscopie NIR
Logiciels utilisés :¶
- Polychromix Method Generator
Objectifs :¶
L’analyse spectroscopique nous permet :- De différencier nos 5 types de plastiques par absorbance
- D’établir une base de données pour le programme Arduino
Résultats des mesures :¶
Part | Fichier | Observation | Image | _.Date |
---|---|---|---|---|
Excel | mesures.xlsx | à compléter | juin 2024 |
(2024/2025) : Résultats en cours. Création d'une base de données pour chaque plastique sélectionné de manière à le reconnaître par la suite avec le Plastic Scanner. Ensuite, essais effectués avec des échantillons de différentes couleurs composés d'un même plastique pour observer si cela influe également sur la mesure. Ces expériences ont également été effectuées avec des échantillons n'ayant pas les mêmes propriétés thermoplastiques ( comme le Polyuréthane, rigide et le Polyuréthane thermoplastique, souple). Les campagnes de mesures effectuées seront ajouté au fur et à mesure de l'avancement du projet dans la partie documentation.
Documentation¶
Thèse du créateur du plastic scanner : https://repository.tudelft.nl/islandora/object/uuid:1fa997b7-c286-4cf3-b3cc-4cfca7cf58f2
Les documents en pièce jointe de cette page ont été téléchargés sur le wiki : https://projets.cohabit.fr/redmine/documents/459
Note : aucune mention de la LED IR 1720nm ! quand on fait une recherche rapide CTRL+F